
Computer-controlled tools have changed high school shop class in ways that many people of a certain age wouldn’t recognize. There are still bottles of glue everywhere, table saws, and cabinets full of pipe clamps and drill bits, but next door there’s now a studio with rows of computer terminals that today’s shop class cannot exist without.
Most shop projects start here, and end anywhere a student can imagine. One Sitka high senior, who is both an aspiring engineer and musician, spent the spring semester making his rock ‘n roll dream come true. KCAW’s Robert Woolsey reports.
In the Sitka High School wood shop…
We all have mixed feelings about shop class. We made cutting boards for our moms, or nightstands that weren’t quite level, while the kid at the next workbench made a mahogany chess board, or a media center for the living room.
Electric guitar solo…
Ryan Mosley has topped them all.
More electric guitar…
This is Mosley No. 1, an electric guitar modeled on the famous Fender Telecaster made in clear dark walnut. It’s got a brushed aluminum pickguard, and an orange epoxy resin inlay with his name “Mosley” and a phoenix in flight.
“I have a phoenix bird that I put on it, because I was born and raised in Phoenix,” said Ryan Mosely, who built the instrument this spring in shop class.
I wasn’t convinced a high school student could make a good guitar, so Mosley and I visited the Sitka Fine Arts Camp, to meet with Sitka’s premiere rock ‘n’ roller.
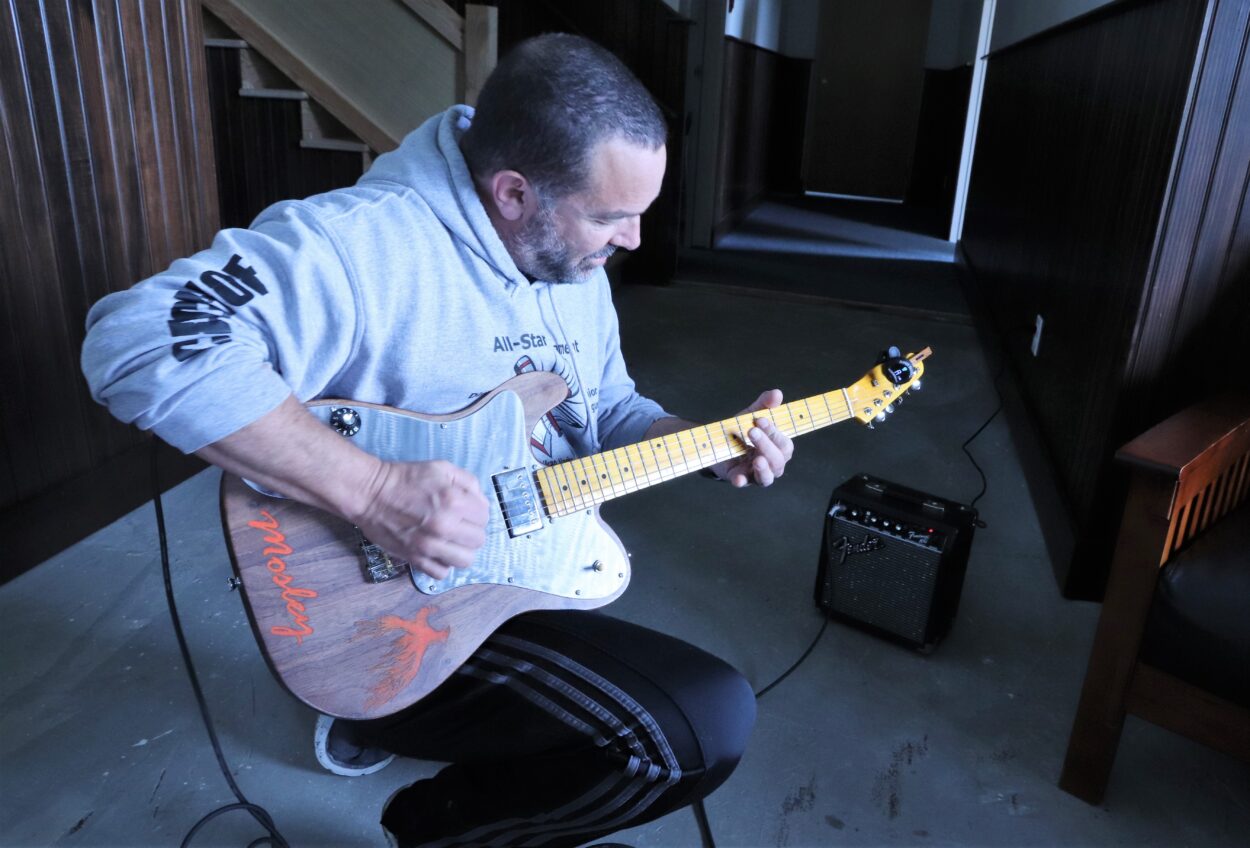
“I’m Joe Montagna. Local Sikka school teacher/guitar player,” said Montagna, stepping out of a classroom where he’s teaching high school students the art of studio recording. “Been playing guitar my entire life, I love guitars. I play lead guitarist in Sitka local cover band Slack Tide. We just do lots of classic rock songs. And.. this is a piece you could put up in a Guitar Center and you wouldn’t blink twice ‘Oh, that’s definitely a school guitar.’ You’d be like, ‘Oh, how much is this one? And then when you picked it up, the real connoisseur will be like, ‘Oh, this thing’s gonna have great tone because it weighs a ton… There’s no name on the top, so I would look down there and see it’s a Mosley. Who’s that? It’s gorgeous.”
So you’re thinking, “Well, he made it on a computer. Of course it’s a good guitar.” But he didn’t make it on a computer – he designed it on a computer, and cut the parts out on a computer controlled router. Everything else – the walnut finish, installing the pickups and electronic controls – was regular shop-class elbow grease. The computer has elevated designs, but hasn’t replaced craft.

“Ryan’s a single Design & Fab II student in a class full of Design & Fab I students, so he’s pretty much an independent studies student,” said Vieira, one of Sitka’s career and technical education teachers. Vieira had the context – and the contacts – to help Mosley create his custom guitar.
“So about six years ago, when we had just gotten this (CNC Router), we hosted a teacher workshop,” said Vieira, “and had a bunch of teachers come down from different parts of the state of Alaska and the Northwest. And they built a bunch of guitars, and the teacher that led that, Cory Torppa, he teaches in Kalama, Washington. And so he wrote the tutorial for this. After that workshop, we were able to write a couple of grants and spend some time together and develop curriculum. And so I’ve, I’ve based a lot of what I do with students on what he was doing with students at that time. So when Ryan expressed that he had interest in doing a guitar, I was like, ‘Oh, I know, just the person.’”
Before school ended for the summer, I visited Mosley in the shop while he worked on the guitar. I watched him cut the curvy telecaster body. Mosley observed as the router bit sliced through the walnut, one eye on the computer monitors next to the machine.

Yeah, it looks like looks like we got a nice nice cut,” said Mosley, vacuuming the sawdust from the finished piece. “So there’s all the pockets. I custom did this off a couple different design references because there’s this tunnel, so the knobs.”
Mosley later cut the guitar’s neck, which was a bit more challenging, as it tapers. With time running out, he bought a ready-made fretboard, and the electronics. In all, he spent around $500 to build a guitar that sells for several thousand.
“How much you want for it?” asks Montagna. “We laugh, but someone must have told that to Les Paul when he made his first guitar. That’s the guy’s name. You know who Les Paul is? Yeah, he literally designed it and went to the company and said ‘Here, Gibson. It’s named after me, you know? 0001.’ I can only imagine what that guitar would fetch today. So hey, you could be the next Les Paul.”
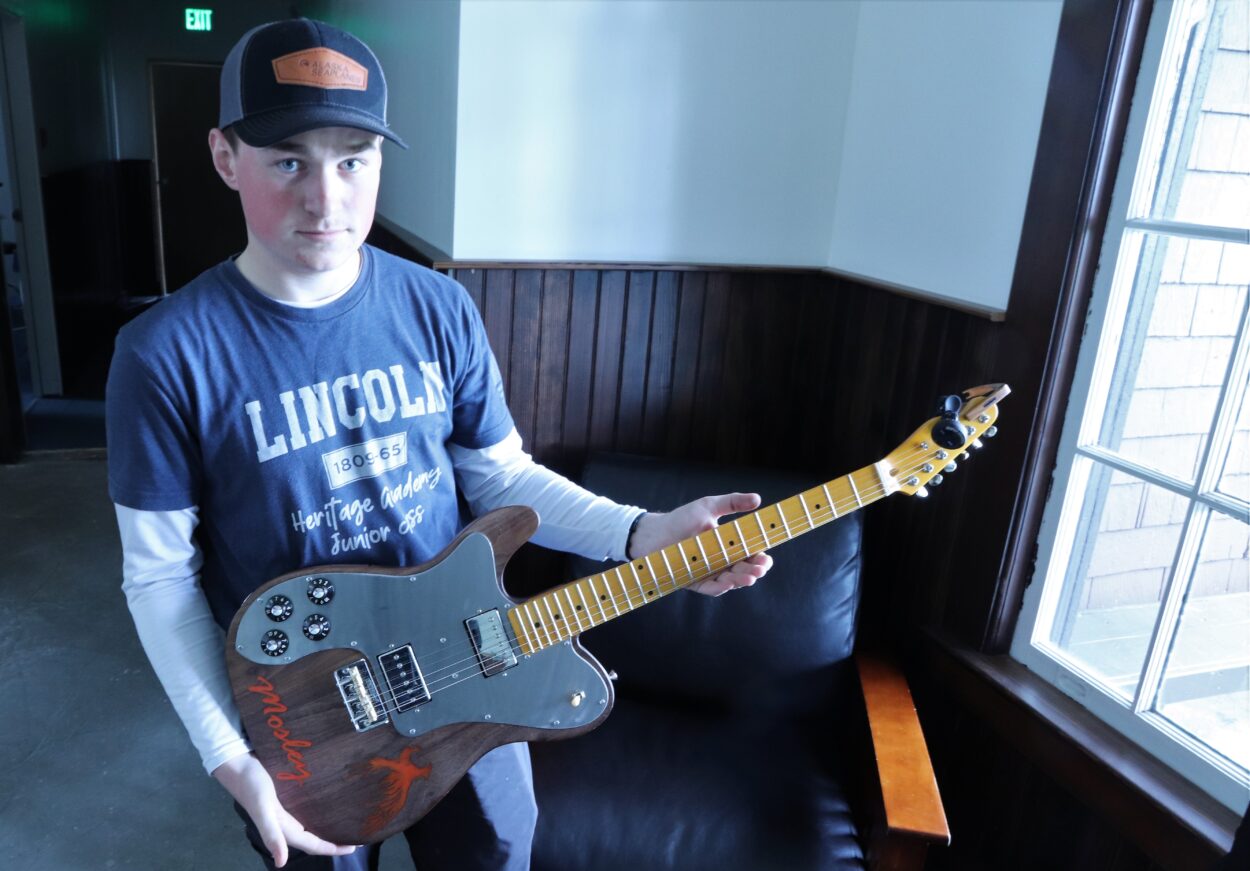
Electric guitar solo…
Mosley is enrolling in an out-of-state undergraduate engineering program this fall. He’ll probably have a roommate who, if fate is kind, had a great shop class too, where he was encouraged to make an electric bass, or at least drumsticks.
Because nowadays, a cutting board just doesn’t cut it.